
製造業DXを進めている企業の約7割が期待した成果を得られていないとされています。生産性向上や競争力強化を目指して導入を進めているものの、実際には「ツールを導入しただけ」「現場との乖離」など、多くの企業がDX推進の失敗事例に直面しています。
では、なぜ製造業でDXが上手くいかないのでしょうか?
本記事では、製造業におけるDX失敗事例を詳しく分析し、陥りがちな課題とその解決策、さらに「2025年の崖」を見据えた対応策まで、具体的に解説していきます。
この記事を読むことで、他社の失敗事例から学び、自社のDX推進における潜在的なリスクを把握することができます。
また、成功に向けた具体的なアプローチ方法も理解できるでしょう。
製造業のDX推進は、もはや選択肢ではなく必須の経営課題です。失敗事例から学び、確実な一歩を踏み出すための指針として、ぜひご活用ください。
製造業で実際に経験した失敗事例をご紹介
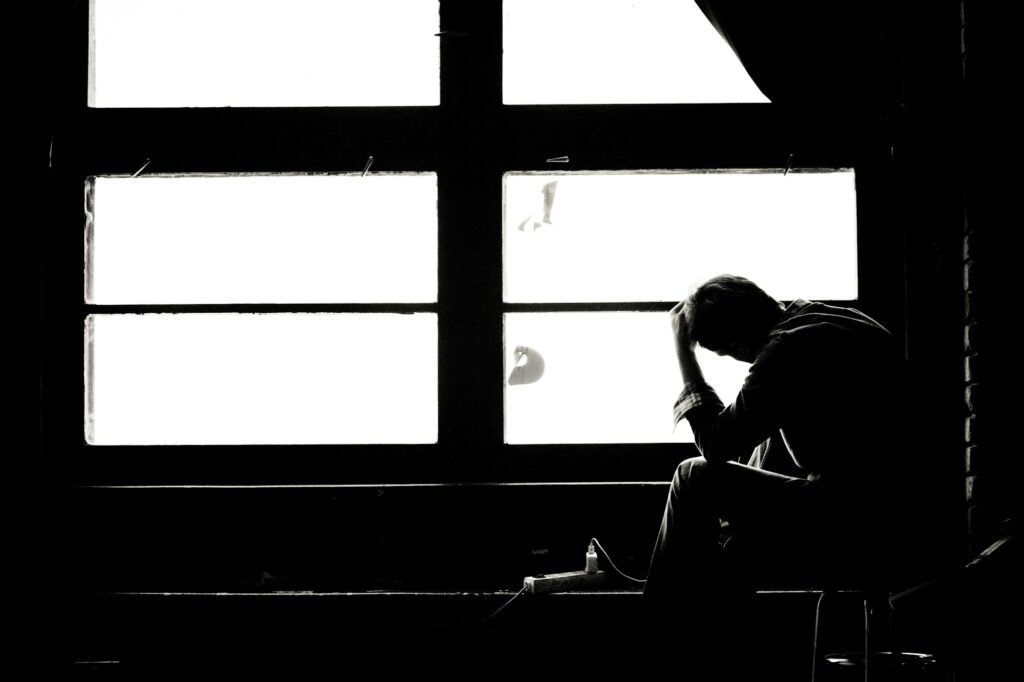
私自身が実際に経験した事例では、生産管理システムを導入したものの「ツールを導入しただけ」という結果に終わりました。現場スタッフは新しいやり方を覚えるのが面倒と従来の手書き記録を続け、結果的にデジタルとアナログの二重管理が発生していきました。
また部署ごとに異なるフォーマットで記録を取っていたため「データがまとまらない」という課題が浮き彫りとなったのです。
さらに責任者不在で頓挫するケースも見られ、導入時の担当者が異動し、その後の運用方針が不明確になったことで、せっかくの投資が水の泡となってしまいます。メリットが不明瞭なまま導入を進めたため、現場はコンフォートゾーンから抜け出せない状態が続き、結果的に部門間の連携不足から全社的な活用は実現できませんでした。
製造業でDX化するメリットとは
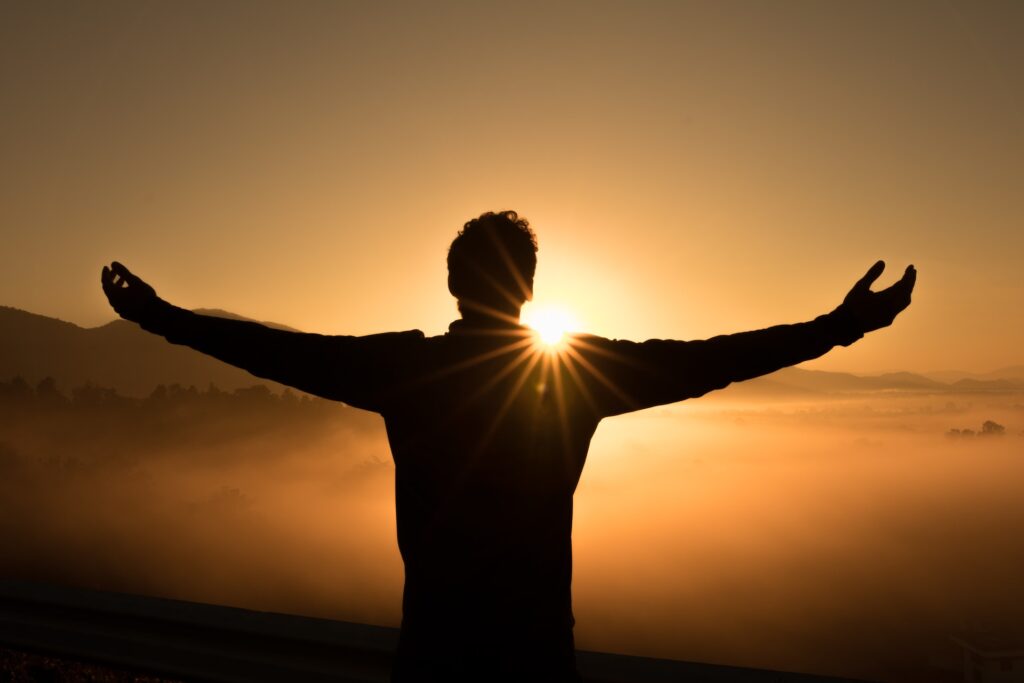
製造業DXの失敗事例が目立つ一方で、適切に推進できれば大きな効果が期待できます。多くの失敗事例を教訓に、確実に成果を上げている企業があるのも事実です。
最も顕著な効果が表れているのが、AIによる生産スケジュールの最適化です。製造業のDXにより、これまで属人的だった生産計画が数値に基づいて最適化され、在庫の最適化による保管コストの大幅な削減にも成功しています。
また、熟練工の作業をデジタルデータ化して保存することで、技術伝承の課題も解決。マニュアルのデジタル化による教育効率の向上も、人材育成の面で大きな効果を発揮しています。
さらに、データに基づく意思決定により残業時間の削減を実現し、納期の正確な予測と遵守も可能になりました。
このように、適切に進められた製造業DXは、生産性向上から働き方改革まで、幅広い領域で効果を発揮しています。
2025年の崖問題
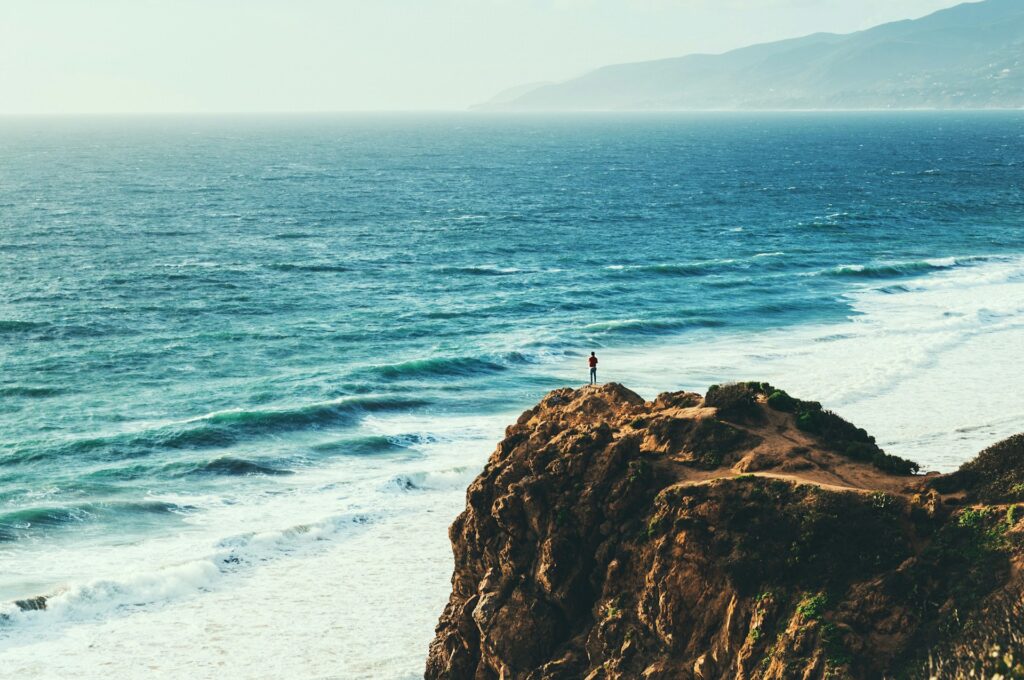
製造業DXの失敗事例を考える上で避けては通れないのが「2025年の崖」の問題です。この課題に対する準備が不十分な企業は、深刻な事態に直面するでしょう。
最も深刻なのがレガシーシステムの問題です。現在、製造業の約8割が1990年代から2000年代に開発された古いシステムを使用しており、メンテナンスが困難な状況に陥っています。このレガシーシステムの存在が、製造業のDX推進を大きく妨げる要因となりました。
さらに、2025年にはIT人材が43万人不足すると予測されています。特に製造業の現場で多く使用されている古いプログラミング言語(COBOL等)を扱えるエンジニアの減少は、DX推進の失敗事例につながるリスクが高まる一方です。
また、2020年以降のデジタル技術の急速な進化により、AIやIoTなどの新技術を活用できない製造業は、グローバル競争で大きく後れを取る危険性が指摘されています。これらの課題に早急に対応することが、製造業DXの成否を分ける重要な分岐点と言えるのです。